ABS System & Fault Finding
The Anti-Lock Braking System fitted to the Scorpio is either the Teves Mk IV or
Mk 20, depending on year. The systems are identical, but the later Mk20 is
updated with smaller control systems and is of lighter weight. The ABS sensors
remained the same throughout production.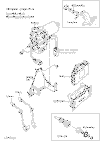
Experienced drivers will know that when the brakes are fully applied the
friction of the brakes will prevent the wheels from turning and the locked
wheels produce a skid. When a front wheel is not turning it becomes a sliding
surface and inertia takes over, the vehicle slides in
a straight line regardless of where the steering wheels are pointing.
Professional drivers use cadence braking techniques to
produce fierce braking and retain steering control, this means jabbing the brake
pedal quickly and forcibly while making steering movements
and this enables the vehicle to be steered around hazards while still
braking.
ABS uses the same effect as cadence braking. It is a peculiarity of the modern
tyre that it produces its maximum retardation just before the point at which it
commences to skid. ABS systems monitor the rate at which each wheel revolves and
when it senses the point of lockup it releases the pressure to that wheel, even
though the driver has white knuckles and is standing on the brake pedal. The ABS
then re-applies the braking force to the wheel, and does this many times a
second, much more efficiently than any cadence braking technique. In the Scorpio
the control frequency of the Teves system can approach 20 Hz (operations per
second). Because of the speed of this pressure-release cycle it is not possible
to use brake drums with ABS: the design of the brake shoes produces a self-servo
action and this would hamper the ABS operating cycle.
Learner drivers are taught the emergency stop and are supposed to feather the
brakes when the vehicle commences to skid to bring the vehicle to a stop without
leaving smoking rubber behind them. With ABS though, the technique is different
- the driver stands on the brake using as much force as he can apply - he will
feel the ABS modulator varying the pressure to the calipers
by a clattering sensation through the brake pedal - but he will retain steering
control throughout. Even on wet and greasy roads, retardation rates with ABS can
be amazing and have saved many lives.
On higher spec Scorpios, the Traction Control system is added. It is
piggy-backed onto the ABS controller and shares the rear wheel ABS sensors,
using input from these to compare the speeds of the driven wheels. If the
separate TCS module detects that one wheel is beginning to spin it uses the ABS
module to brake this wheel and a servo attached by cable to the throttle body
forces the throttle to close, so that the driver feels the accelerator forced
upward against his pressure. This intervention ceases as soon as the controller
detects that order is restored. The module defaults to 'ON' - so that the TCS is
not operating when the button in the centre console is pressed and while the
light shows in the instrument panel.
The ABS system on the Scorpio consists of a Module, Modulator and four wheel
sensors.
The ABS module receives the signals produced from the sensors in each wheel hub.
The sensors are magnets surrounded by a coil, and are mounted close to an ABS
sensing ring which revolves with the road wheel. These have segments, so that as
the wheel turns the protrusions produce a magnetic flux in the sensor which is
detected by the module. It is by comparing the frequency of these signals that
the module can determine which of the wheels is about to lock up and will order
the modulator to release the brake pressure to the affected wheel.
The Modulator is connected directly to the brake servo, and receives the full
brake pressure applied via the servo from the driver. This pressure is diverted
through three separate channels one to each
front wheel and one circuit to the
rear, so that although there are sensors for each rear wheel both rear brakes
are modulated as a pair. On a given signal from the module, the modulator
operates the solenoid valve and release the brake pressure from one or more
wheels. The ABS modulator actually contains its own pump which rapidly
increases the pressure inside a wheel cylinder, depending on the pressure applied
to the brake pedal. In this way extremely powerful braking effort is applied at
a frequency approaching twenty times per second. People
who do not understand ABS often state that ABS does not make braking distances
shorter but merely allows for steering while braking, and this is simply not
true - ABS will bring a car to a halt in a shorter distance regardless of the
type or condition of the road, in dry, wet and even on ice, because it keeps the
tyres in a cycle near the point of maximum retardation with an efficiency beyond
any human capability. It is for this very real safety advantage that from the
1st July 2004 it will be unlawful for a new car without ABS to be on sold in the UK.
Fault Finding, Teves MkIV
There is some mystique about the ABS system, but it is simple and robust. The
Module very seldom causes trouble, unless it is spiked by careless welding or
electrical procedures. Modulators have been known to fail, but faults are much
more likely to be with connections or sensors. Before
resorting to an expensive ABS diagnosis there are simple checks that can be made
which are often all that is required.
The ABS light might appear to be useless as a diagnostic tool, but it can tell
us two things of vital importance in fault-finding. It should come on when
starting and go off after the few seconds of self-testing.
If the ABS light stays on then it indicates a hardware failure rather than a
signal loss from a sensor. Experience shows that the fault is most likely to be
a faulty sensor - they are reliable units but they can fail.
If the light goes off, but lights again within a few moments of moving off, it
often indicates that a sensor which passes the start-up test is now failing to
send an adequate signal. This is most likely to be dirt collecting in the ABS
sensor area or corrosion of the sensing surface and is preventing the sensor
from detecting the sensing ring, but it could also be a loose connection which
is vibrating or damp and interrupting a signal. If the ABS light comes on
briefly on damp mornings it is most likely to be dampness affecting a multiplug,
and experience suggests it is most likely to be at the front. During the second
part of the moving test, the ABS control module fires each modulator solenoid in
turn and checks the pressure. A problem with a solenoid will illuminate the ABS
light. This test may be detected occasionally if you are applying light
pressure on the brakes at parking speeds, by an odd sensation on the pedal under
your foot.
While the ABS light stays on, the ABS module is not operating at all, but normal
brake pressure will still be applied from the brake pedal. If the vehicle is
equipped with Traction Control the TCS shares the same
light as the ABS and a fault in either module will keep the
light on.
Connections
The Modulator is connected via a multiplug to the Module and this can be checked
quite easily. On some vehicles an additional connection is made to the Modulator low down on the
drivers side of the engine compartment at the bottom of the McPherson strut
turret. This connection is in the road spray and baked by the heat of the
manifold and should be the first connection to be checked, particularly if the
ABS light shows intermittently - although some owners of later cars have not
been able to find this connection.
Pull off the connections to the modulator and
examine each for wetness or corrosion. Use waterproof grease and remake the
connection. After each check, try the ABS system again on the ignition switch -
if the ABS light then goes out you will know which connection was at fault.
Return to that multiplug, clean the inside and pins as much as possible and use
waterproof multiplug grease when reconnecting.
Sensors
The rear wheel sensor wiring come through the wheel arch through a grommet into
the passenger compartment, beneath the rear seat cushion and under the carpet.
Once the seat has been lifted the connections can be checked, but being in the
dry they very seldom give trouble. It is a simple
matter to connect a voltmeter to each sensor and check for a resistance. Compare
them - but generally if a sensor has failed it will show as open circuit, and if
this one sensor is replaced it is very probable that normal service will be
resumed, so if an open circuit is found that sensor must be replaced wherever it
is.
The connections for the front sensors are in the wheel arch, clipped up to the
inner wing behind the MacPherson strut. The multiplug can be checked there too
and the sensors checked for a resistance at the same time. Once again check the
system with the ignition key after each operation.
If work has recently been
carried out on a wheel hub in which you suspect that a mechanic has been hitting
the hub with a hammer, check that hub first. ABS sensors are vulnerable to hard
shocks and you may well find that the sensor has gone open-circuit. This may not
happen at once, but often a couple of days later, when a sensor, weakened by the
shock of hammering, then goes open-circuit over a bump or ramp in the road.
The hub bearings keeps the
sensor ring and the sensor itself at a suitable distance. If a bearing is
failing the shaft may be oscillating and this is likely to fail the moving test
- the ABS light will come on after moving off. If during the checks a hub is
found to be worn, particularly at the rear, then this wheel bearing should be
replaced first since it is probably the cause of the ABS error.
Because the TCS uses the rear ABS sensors, if
both lights illuminate, check the rear sensors first
Dirt/Corrosion
Particularly in the event of a ABS light
coming on soon after motion has commenced, the sensors will each need to be
removed and checked for dirt/corrosion or damage.
Front Sensors.
Raise the front of the vehicle, remove the
front road wheels. The ABS sensor is set into the front hubs at 3 o'clock,
behind the brake disk. Clean the area around the sensor so as not to admit dirt,
remove the bolt and withdraw the ABS sensor. Check for corrosion/dirt or damage
and replace. Torque the mounting bolt to 14Nm. Check the ABS light with the
ignition key after each inspection.
Rear Sensors.
Raise the rear of the car and remove the road
wheels. Remove the disk caliper by removing the two bolts at 10 and 2 o'clock
into the rear of the caliper. They are protected with plastic plugs - don't lose
these.
At 12 O'clock the sensor can be seen mounted into the rear hub. Carry out the
same check for dirt/corrosion and replace. Torque the mounting bolt to 14Nm and
replace the caliper, torquing these caliper bolts to 56Nm and do not forget to
replace the plastic covers.
Note: some
owners have reported that the ABS sensors have corroded into the hubs and cannot
be removed for checking without causing damage. If this is the case it is
probably more economic to have the ABS system interrogated by a
properly-equipped local garage without going further. Typical rates for a
reading for fault codes have been in the £40 to £60 area. Main Dealers are
typically £90.
Our Vehicle Explorer software, together with a PWM/ISO combi lead can now read
ABS diagnostics, thanks to work by Mark P and Alex Peper in the US. If you
already own a single lead, you may send it back to the US in return for a combi
lead, and the latest version of Vehicle Explorer has been updated to recover
Trouble Codes from the ABS module.