Mark the relative position of brake disk and hub and replace one wheel nut to
stop the disk falling off. |
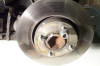 |
In
theory there should be the spring clip but these are often missing. Unbolt the
caliper assembly (2 off 15-mm. bolt's) and hang it safely out of the way.
Obviously you can't hang it on the suspension so I had prepared a Ty wrap loop
and nipped it behind one of the Torx screws that hold the inner wheel arch. Make
sure that the Torx screw isn't going to strip out of the plastic insert, you
don't want the caliper falling on the floor. (I found several of my inserts
were stripped and replaced them earlier in the year, they are quite cheap.) A
second Ty wrap looped through the first and then through the caliper holds it
nicely out of the way.
You will probably want to clean out the mud and Waxoyl the turret later on so
remember to cover the caliper in newspaper before you do. Remove the disk.
|
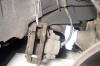 |
In theory you need to remove the anti-lock brake sensor
(shown with its bolt partly removed) from the spindle carrier
but mine was so tight that I felt I would break it so I chose instead to unplug
the sensor from the connector mounted on the wheel arch. Use a small screwdriver
to "trip the catch". Tape up both ends to prevent muck getting in and unclip it
from the brackets on the wheel arch and the strut. The downside of this method
is that it leaves the wire somewhat vulnerable so keep it out of the way and
protect it. The bracket on the strut can be removed at this stage. You will need
to mount it on the new strut and there are two possible positions so note
carefully where it goes.
|
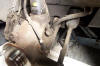
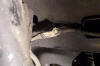
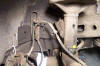 |
Remove the two nuts from the link between the anti roll bar
and the strut. The top nut is 15 mm. and the lower one 18 mm. As soon as
they stop nipping, the ball joints will rotate. Fortunately Ford have
thought of this and provided ways to stop them. Hidden in the end of the top
stud there is a 5 mm Allen socket but you will need to clean the muck out to
see it. The lower one has a fairly obvious 17 mm. flat so you'll need a
suitably thin open-ended spanner. (The top one can actually be left until
the strut is on the bench if access is difficult)
Remove the 3 off, 13-mm nuts and washers that hold the top of the strut and
replace a couple of the nuts finger tight. Make sure that they are well on
as the strut itself is very heavy, I could hardly lift it. Later on you will
need an assistant to remove these nuts while you support the strut and
remove it.
|
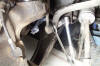
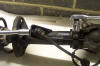
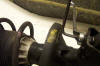 |
Next remove the nut from the track rod end. To remove the
taper itself you'll need a suitable splitter. I have, in the past, managed
without but it's just not worth the risk of damaging the gaiter. I bought
the Sykes-Pickavant tool from Halfords for about £15, which seems to work
well. To protect the gaiter after removal I cut out a piece of cardboard. At
the same time I made a couple of "U" shaped cardboard masks to slip round the
bottom joint and protect its gaiter. The bottom joint is not available
separately from the wishbone (which costs about £75) so you don't want to
damage it.
|
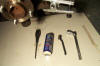 |
Remove the nut and bolt from the bottom joint. I found that
the 18-mm. nut came off fairly easily but despite using a high-quality
brand-new Torx bit I could not turn the bolt. Eventually, with about 150
pounds foot of torque, there was a crack as the spines sheared. Oh dear!
More of this later.
Once the bolt is removed, the shaft of the ball joint is still a tight fit
in the spindle carrier so I came up with a very useful trick. Place a washer
and one of the old 13 mm nuts on top of the shaft and use the track rod end
splitter to force it down. When the nut has disappeared inside, back it off,
add another nut and repeat. This is much easier than trying brute force.
Another tip is that the wishbone will definitely swing down far enough to
clear. Originally, when I was struggling to get it out, I thought that this
was the problem and tried jacking the strut back up but this is not to be
recommended and is not necessary anyway.
|
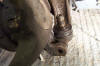
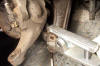 |
With the assistance mentioned earlier the strut can now be
removed and placed on the bench to separate it from the spindle carrier.
Remove the 18 mm. pinch bolt and knock the casting off using a soft faced
mallet and tapping each side alternately. If you open the gap gently with a
cold chisel it will ease the job but be careful, cast-iron is brittle. |
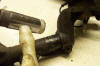
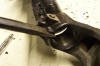 |
Now the bit I hate, compressing the spring. You cannot be too careful here,
there is a huge force on the spring and you need to compress it further.
Remember it normally supports over a quarter of a ton of car and perhaps twice
that under load so there is an immense amount of energy stored here. The big
danger (apart from a failure of the compressors) is that one of them will slip
round the other side part way through the compression. It all happens very fast,
there is a big bang and the spring ends up like a banana. All very frightening.
Do not ever put your hands in between the coils or spring seats. I nearly lost
my fingers.
|
I haven't a perfect solution. I bought a pair of new spring compressors and used
them as well an older pair I already had but using four isn't ideal because one
keeps coming loose as
another takes the load. With hindsight, and I haven't actually tried this,
perhaps three is the ideal number. Even with two it's important to keep them "in
step" a little tightening of each at a time and don't be tempted to tighten one
a lot or those narrowed coils become a ramp that the other compressor is all too
keen to slip down.
|
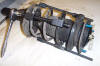
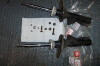
|
Once the spring coils are safely restrained (check and double check, tapping
gently) remove the nut from the top of the piston rod. You need to prevent the
rod turning with a 7 mm Allen key so a ring spanner is called for, not a socket.
This is an unusual size, 21-mm. I had to buy one specially.
It's now a simple matter to lift off the retainer, the top mounting, the thrust
bearing, the upper spring seat, bump stop and gaiter. I found the last three
stayed joined together, which is fine. Note how the spring fits into notches in
both top and bottom seats. I marked all the bits with paint to enable correct
reassembling.
All these (in reverse order) are placed on the new strut and the (new) lock nut
retightened. You can now (equally carefully as this is where I got blasé and
trapped my fingers) relax the compressors. Check everything seats correctly and
start to breathe normally again.
Reassembling is pretty straightforward I replaced every nut and bolt with new
ones, they are mostly locking nuts so shouldn't be reused and only cost about £4
a side for the lot. Strangely the spindle carrier pinch bolt's are supplied with
the new struts but the lock nuts for the top of the piston rod are not and had
to be ordered specially. I put plenty of grease round everything; in particular
I packed the slots at the top and bottom of the spindle carrier where they clamp
on to the strut and bottom joint shaft respectively. I think that these slots
are the reason it gets so rusted up. Normally a bolt head is fairly well sealed,
as is the thread, but these slots allow water into the middle section of the
bolts. Unfortunately I'm not sure what to do regarding grease on those bolts
which Ford supply preloaded with what I take to be thread locking compound? |
Torque Settings (Nm)
Component |
Nm |
Strut
piston rod top lock nut |
59 |
Spindle
carrier to strut pinch bolt |
85 |
Anti roll
bar Link Assembly to Strut |
48 |
Strut to
wing turret (3off) |
46 |
Lower arm
(wishbone) to spindle carrier |
80 |
Anti roll
bar to Link Assembly |
80 |
Track rod
end retaining nut |
28 (or 37
Needs investigation) |
ABS sensor
to spindle carrier |
10 |
Brake
caliper bracket to spindle carrier bolts
(NOT caliper to bracket) |
56 |
Road Wheel
Nuts |
85 |
|
|
Item/Code |
Description |
QTY |
Unit Price |
My Notes |
5030214 |
SHOCK ABSORBER |
1 |
51.48 |
24 valve |
5030217 |
SHOCK ABSORBER |
1 |
51.48 |
24 valve |
1138220 |
BOLT |
2 |
0.49 |
Bottom joint pinch |
6517149 |
NUT |
4 |
0.36 |
Bottom joint pinch and Link bottom |
1549071 |
NUT |
6 |
0.29 |
Top mount |
6194242 |
NUT-HEX . S/LOCK |
4 |
0.49 |
Track rod and Link top |
1668038 |
NUT-HEX |
2 |
0.45 |
Strut piston rod top |
6136989 |
BOLT-HEX . HEAD |
2 |
0.95 |
Strut / carrier clamp |
Last item was ordered but are no longer
available as they are supplied with the strut.
Prices shown are each, excluding VAT and discount |
Incidentals: - |
The thrust bearing from the top of the strut seemed to be
gritty so I stripped it down, cleaned it and re greased. The two plastic
halves can be carefully prized apart leaving two (rather sharp edged) metal
tracks, a plastic cage and 48 steel balls. These are loose so be careful
that they don't go everywhere when you open it.)
|
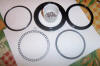 |
And what about that seized bolt? I tried cleaning the rust off and drenching
with Plus Gas. I tried belting the end with a big hammer but was frightened of
damaging the lower joint, which I assume, is nylon inside. I didn't try heat
because of the proximity of the rubber. I tried two lock nuts on the free end
but they just spun back off. I tried force with a mole wrench, which of course
destroyed the thread. I even considered removing the strut complete with the
wishbone attached. (The bolt's that hold on the inner
end of the wishbone seem quite accessible.) In the end I resorted to carefully
drilling the bolt out from the head end. Start with a small drill and then
increase in size. Don't make the steps in size too small of the drill will
snatch. Use plenty of lubrication and take it very steady making sure you keep
down the centre the bolt. Eventually when most of the core had gone I
sheared off the head and was able to knock out the remaining threaded bit. I did
think at one stage that the bolt was threaded into the spindle carrier but it
isn't, it's just a slide fit (at least when its new). The one on the other side
of the car eventually knocked out after much twisting to free it up.
|
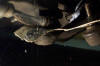 |
It took most of the day to do each side so was it
all worth it? Yes, very much so, the car feels to respond much better to sudden
maneuvers at speed (although obviously it's still a big car.) I've always been
concerned about this aspect of my Scorpio, and changed the rear dampers earlier
in the year, (which is just as well when we had a blow-out at high-speed on the
French motorway.) Also there's now almost no overshoot at all on a bounce test.
|